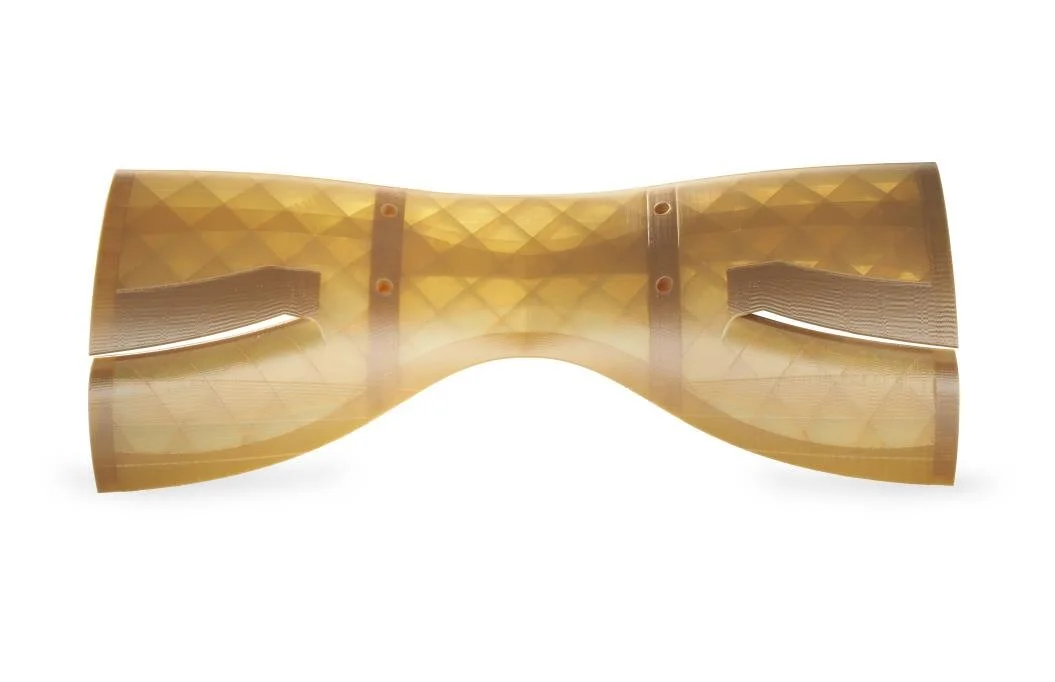
ULTEM-9085
Ultimate thermoplastic - certified for Transportation, Rail, MedTech.
ULTEM™ 9085 resin filament is a PEI (polyetherimide) thermoplastic FDM material. It features a high strength-to-weight ratio, high thermal and chemical resistance, and meets multiple aerospace and railway industry standards for flame, smoke and toxicity (FST) characteristics (UL 94-V0 rated). Typical applications include production parts and functional prototypes. Available colors are natural and black.
Commonly used in the automotive, aerospace, military, rail industries, MedTech and Pharma production. ULTEM offers excellent mechanical features, an outstanding traction strength and a temperature resistance up to 216 °C. FAA Flammability certificate FAR 25.853. EN45545-2 rail certification guidelines for smoke, toxicity and fire. Complies with ISO standards ISO 10993 for Biocompatibility in production of Medical End-use Parts. Pieces manufactured with this material can be sterilizable through steam autoclaving, gamma rays or ethylene oxide (EtO).
ULTEM 9085 Material Data Sheet: [DOWNLOAD]
Components for Pharma Equipment
ULTEM-9085 vs. Stainless steel 316L
ULTEM™ 9085 resin meets ISO 10993 for Bio-compatibility and can be exposed to Gamma Radiation, Steam Autoclaving and EtO. Material certification is a key process in the manufacturing of Medical and Pharmaceutical components. It touches virtually all sectors including Equipment for Medicine production, packaging, tools, instruments, etc. Sterilization is the core challenge to meet the Industry requirements, which until recently could only be cost-effectively achieved with Stainless steel 316L components.
Examples of 3D manufactured parts for Pharma Industry include Disposable filter cartridges, brackets, clamps, silicone tube connectors, buffer containers. Benefits from using 3D Bio-compatible Parts are: reduced the time to get a facility up and running, compliance with cleaning requirements, allowing flexibility with a modular approach. Examples of 3D manufactured Medical Devices initial include surgical cutting guides for orthopedics (knee, hip, bone fractures) and dental restorations, as well as personalized implants that intimately fit a patient. Benefits from using 3D Bio-compatible Medical Tools – Ultra fast design validation, pre-clinical or clinical trials, and early commercial customer feedback before investing in expensive Stainless Steel tooling.
Rail & Transportation After-market parts
ULTEM™ 9085 resin meets EN45545-2 rail certification guidelines for smoke, toxicity and fire, a requirement for train components in Rail Industry. The main benefit of FDM technology and ULTEM-9085 thermoplastic for Rail industry is the speed of production of large-size heat and chemical resistant After-market parts, ensuring that total functionality, safety and repeatability are upheld. Common application of AM in Rail industry: HVAC components for Air vents, ducts, cooling of Ventilators, Rotors, engine compartments with high exposure to Heat, chemical and toxic particles. Cost efficiency of AM derives from manufacturing Existing After-market parts, where original Spare part supplier does not ensure timely production, and storage costs in warehouse are not justified. ULTEM-9085 can replace many HVAC parts that have previously been made of metal sheet, or CNC machined. Multiple components assembled together can be 3D printed as single part, without manual assembly work, from lightweight thermoplastic instead of Steel.
This allows Railway Maintenance Managers to build a digital inventory of obsolete After-market parts, ensuring spare part needs are fulfilled on-demand regardless of the particular train model or its age. By generating 3D models of parts, the Inventory becomes available on-demand manufactured with certified train-ready part with ULTEM-9085.
Rail companies in Europe using FDM technology and ULTEM-9085 include Bombardier Transportation, Deutsche Bahn, Angel Trains in UK, Latvian Railroads Rolling Stock.
Factory Floor Tools
ULTEM-9085 vs. Aluminum
Additive manufacturing becomes cost-competitive with CNC machining of Tools for Factory Assembly and Production, because it helps to overcome the limitations of CNC machinery when it comes to design complexity, customization and production speed. Also provides reduced weight of tools. Tools from ULTEM-9085 with metal inserts, such as nuts and washers can be printed and combined in one Tool. Due to the complexity of certain components, much of what we produce with FDM technology wouldn’t be possible through other more basic machining methods.
From a cost perspective, it is around 50% less expensive to produce production tooling or parts with FDM additive manufacturing compared to traditional machining. In addition, there is less capital and less labor, faster Tool production lead-time, less machine downtime. The push-and-play element of the technology means that once a print job has been set to run, the operator can
Main application for ULTEM-9085 on Factory floor is manufacturing of replacement production tools and parts in high-performance thermoplastics that perform in the same way we would expect of a traditionally manufactured equivalent, for example robotic grippers, assembly guides, test rigs, gluing jigs and fixtures. Main benefits are time-saving and cost-saving. It avoids lengthy manufacturing times associated with traditionally produced tools, and bypasses costly machine downtime associated with the wait for replacement parts. Instead, it allows to ensure continuous production and little to no machinery downtime.
For example, manufacturing a test rig components by traditional means would require individually machining each part. This process poses several drawbacks: long lead-time for fabrication (4-10 weeks), material waste associated with machining, higher material costs.
Test rig manufactured with ULTEM™ 9085 resin, a high-strength PEI thermoplastic offers the following benefits:
significantly reduced lead time,
lower material cost,
greater design freedom,
high-strength and high-performance material.
To fully replace aluminum for test rigs tensile strength requirements.
3D printed layup tools from ULTEM™ 9085 resins are used for the production of carbon-fiber parts. Process required materials that can stand up to the high temperatures and pressures of the layup process as aluminum tools do. The 3D printed molds offer extremely high heat resistance and thermal stability, meeting requirements for high-performance carbon-fiber parts in timeframes not possible with CNC composite tools. Production of composite layup tools from ULTEM takes just a few days, compared to 2-3 weeks with CNC machining.